United States Air Force Test Pilot School partnered with the 586th Flight Test Squadron at Holloman AFB and NASA’s Armstrong Flight Research Center to test the new use case of the AgilePod using a T-38C.
The United States Air Force Test Pilot School’s research division, in collaboration with the 586th Flight Test Squadron at Holloman AFB and NASA’s Armstrong Flight Research Center, recently conducted a flight test campaign to validate the use of the new AgilePod. Named “Have STRAINger Things,” the tests demonstrated AgilePod’s effectiveness for rapid airborne experimentation, reducing traditional lead times and costs in flight-testing.
The name “Have STRAINger Things” is inspired by the popular Netflix series “Stranger Things.” This clever play on words ties the name of the test campaign to the concept of strain sensors being used in the research, emphasizing both the novelty and the technical nature of the project.
While traditional copper straining has been used for flight test instrumentation since the 1930s, it requires significant time and effort to install resistive strain sensors on aircraft. NASA’s Armstrong Flight Research Center developed a unique Fiber Optic Sensing System (FOSS) that uses dedicated fiber optic strain sensors and provides critical data points more efficiently.
According to the USAF, the proximity of Air Force Test Pilot School and NASA AFRC at Edwards facilitated daily discussions about testing the FOSS system airborne. Simultaneously, the 586th FLTS, part of the Arnold Engineering and Development Complex in Tennessee, advanced their AgilePod Lab, enabling quick-turn capability for carrying special payloads for data evaluation. A trilateral agreement was formed, benefiting all parties involved in the test.
“The 586th FLTS is unique among flight test squadrons as we don’t just support one platform like the F-35 or B-2,” noted Capt. Nathaniel Raquet in a public release. “Our primary goal within AFTC is to support rapid experimentation and prototyping. This project also allowed us to test and utilize the new AgilePod Lab, paving the way for serving a variety of future customers.”
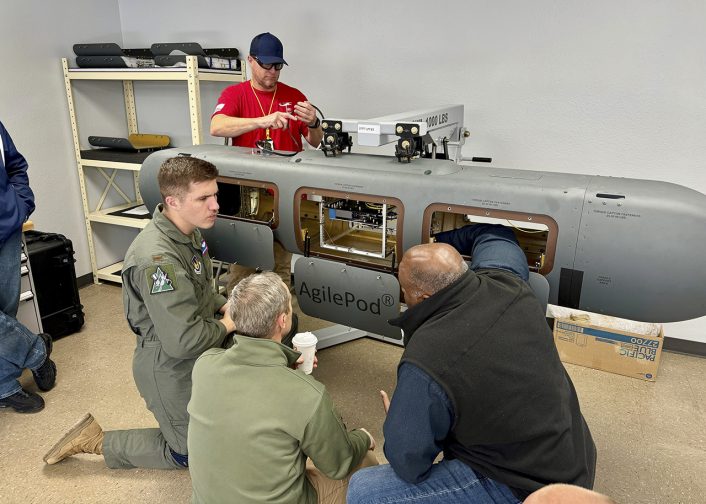
Strain sensors are typically used in load, buffet, and fatigue testing of new aircraft or in certifying new stores on existing aircraft. Stress and strain at critical aircraft and pylon/wing-mount structure points are measured to analyze the response to control deflections from the pilot or flight control system.
New aircraft designs often include thousands of resistive strain gauges, each requiring two electrical connections, signal conditioning, and data recording. This setup adds weight and limits the utility of test aircraft for other flight tests. In contrast, fiber optic strain sensors offer increased sensing bandwidth, electromagnetic interference compatibility, and the ability to apply multiple sensors to a single fiber.
Using the AgilePod mounted on a T-38C, the campaign included six test flights combining engineering flight test techniques with two primary experiments. The first compared fiber optic strain sensors to legacy resistive strain sensors. Both types were installed on a simple cantilever beam weighted on one end. By inducing controlled deflection/strain through aircraft maneuvers, the test team verified sensor performance. Additional fiber optic sensors were added to the AgilePod’s structure to test FOSS for future aeroacoustics and environmental tests, despite lacking reference sensors for comparison.
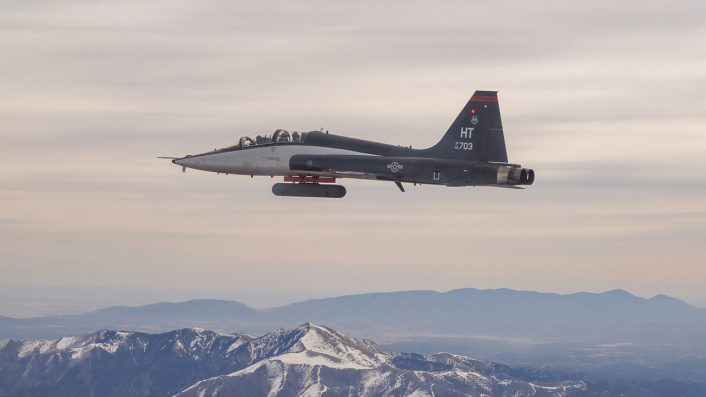
Successful campaign execution will guide further instrumentation using fiber optic strain sensors for flight tests and other applications.
“Without the partnership between NASA with FOSS and the 586th FLTS with AgilePod, we would have had to allocate significant budget and physically modify a T-38 aircraft for sensor installation,” said Wei Lee, Director of Research for the Air Force Test Pilot School. “This unique partnership exemplifies how technology rapidly improves flight test execution, ultimately providing new capabilities to both warfighters and commercial customers faster.”
AgilePod
The U.S. Air Force has been working on a family of AgilePods of different sizes for several years now. In 2018, the program ran by the AFRL Sensors Directorate Blue Guardian team completed inflight testing of a mini-AgilePod on a DC-3, Textron Scorpion, and MQ-9 Reaper.

More recently, we reported about the use of the AgilePod-26 for to test advanced communications capabilities on the B-52 as part of the TENTaCLE (Tactical Edge Network Targeting in a Contested Long-Range Environment) program.
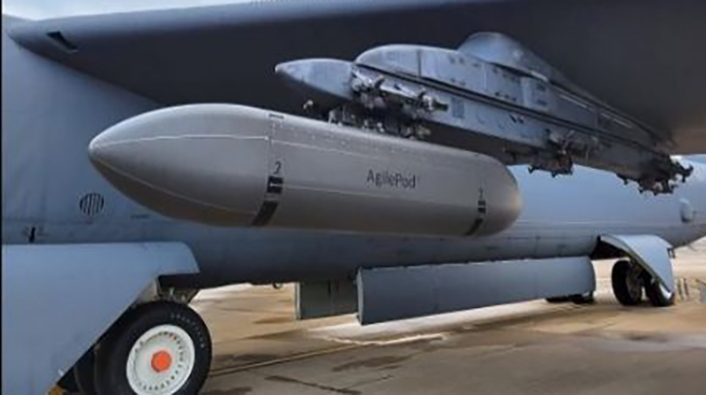
Generally speaking, the AgilePod is an Air Force-trademarked, multi-intelligence reconfigurable pod that enables flight-line operators to customize sensor packages based on specific mission needs.
The AgilePod, available in various form factors, enables rapid integration of new technologies onto existing certified platforms. This innovation streamlines what used to be a lengthy process, eliminating the need for developers of novel airborne data and communications systems to engage with multiple aircraft procurement and sustainment offices and design custom packaging solutions. Previously, this integration process could take 5 to 7 years before initial testing on a single aircraft type.